Why Are Custom Boxes More Expensive Than Standard Boxes?
Explore why custom boxes come with a higher price tag than standard boxes. Understand the value of tailored packaging solutions for your business needs.
Start Customizing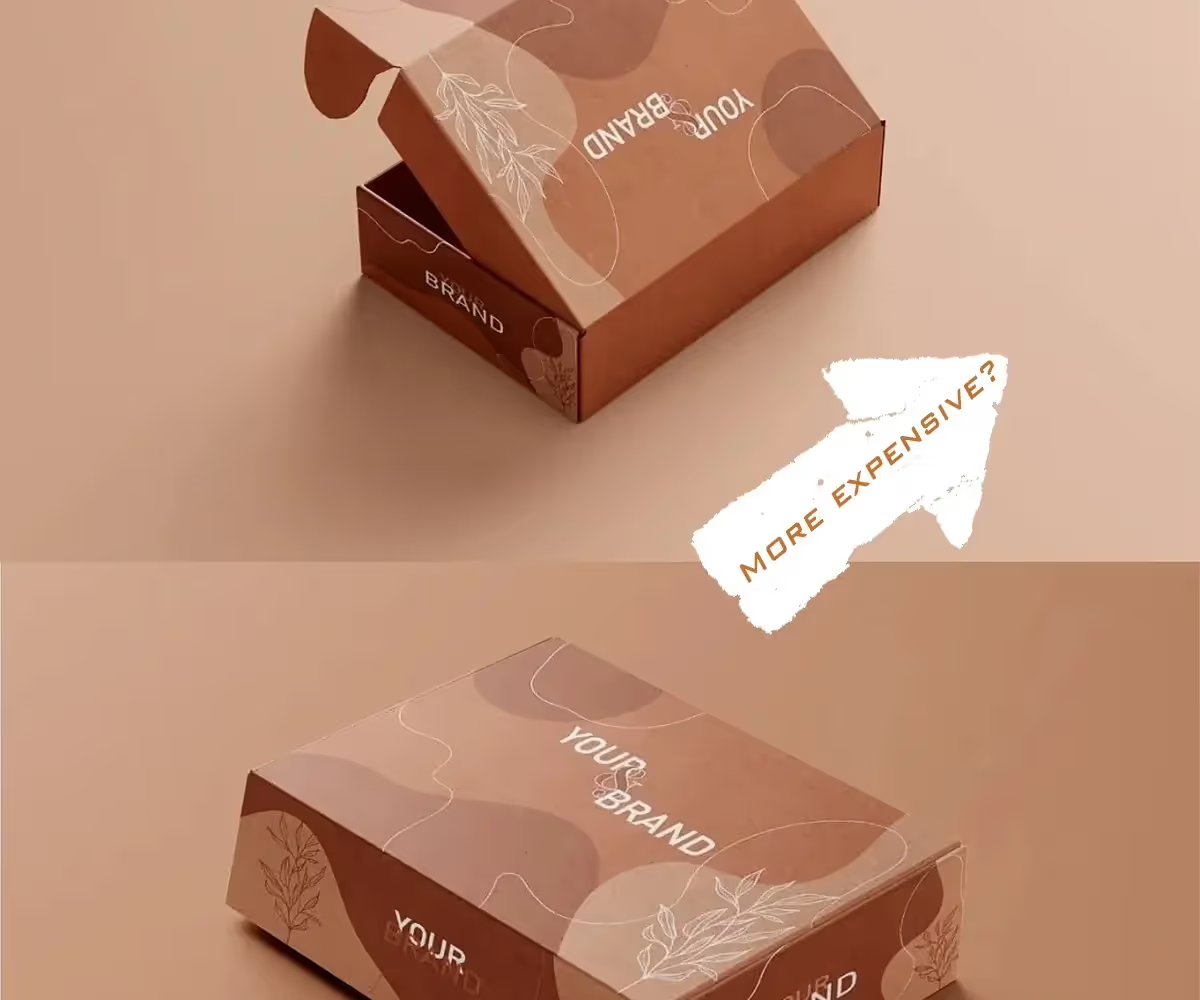
Table of content
In the packaging industry, custom boxes are popular for their unique designs and brand-specific personalization. However, many customers find that custom boxes are significantly more expensive than standard boxes, and the unit price rises as the order quantity decreases. Why does this happen? This article will delve into the factors behind custom box pricing to help customers better understand the cost structure.
Design Costs: Creative Investment from Scratch
Unlike standard boxes, custom boxes require a design process that starts from scratch. Custom box design needs to meet specific brand requirements, including choices of material, color, size, and printed patterns. This design process isn’t a simple adjustment; it requires a completely new approach based on the product’s characteristics and brand positioning. The time and effort invested by professional designers must be factored into the cost.
Especially if the client doesn’t have ready-made design files and requires design services from the manufacturer, this cost will increase further. Design fees are a one-time investment, but the fewer the boxes ordered, the higher the design cost per unit. This is why, when the client lacks a design plan, the unit price rises significantly due to the complexity and additional cost of design services.
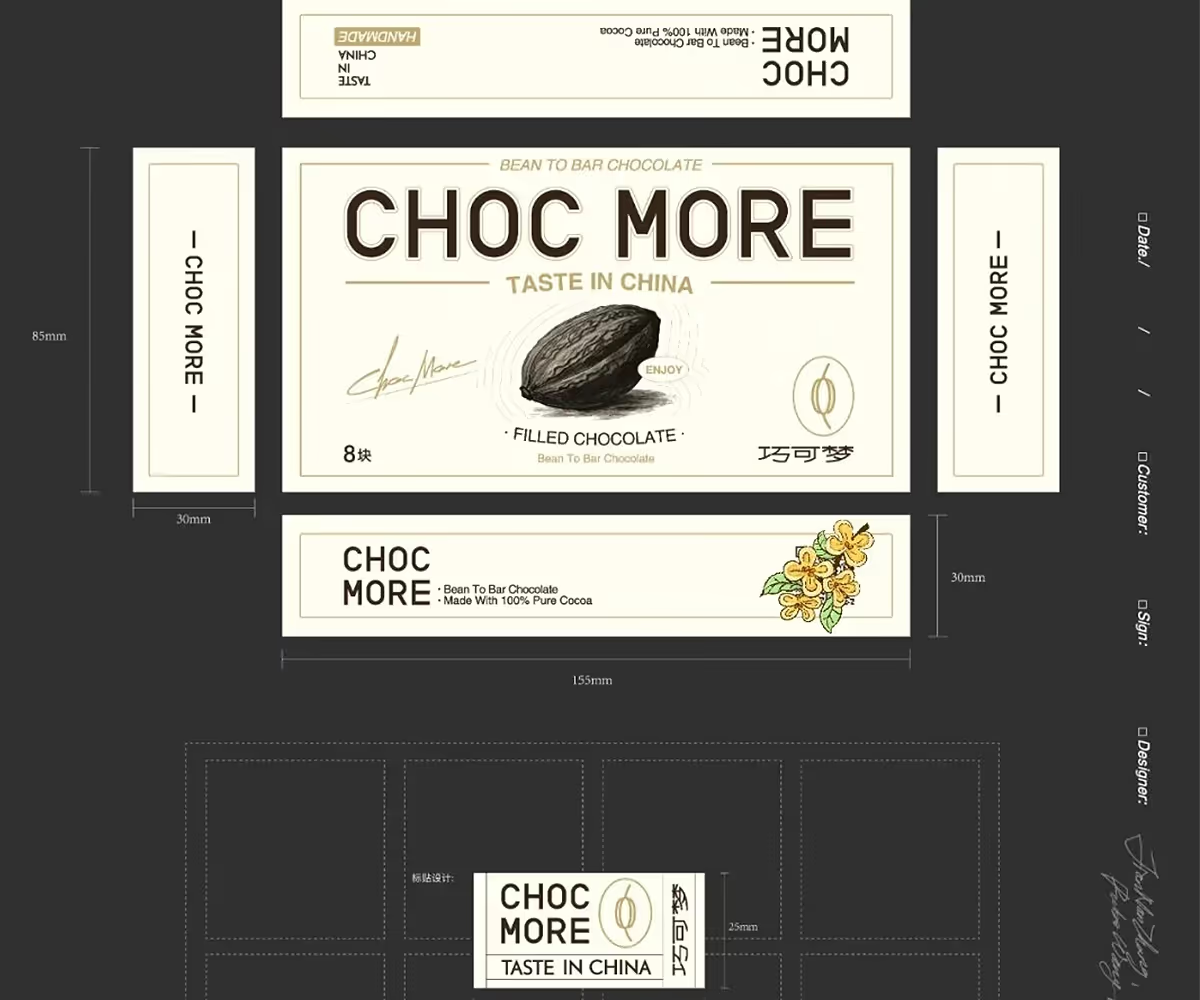
Sampling and Mold Fees: Custom-Made for Unique Designs
Custom packaging boxes require sampling to ensure the final product aligns with the design concept. Sampling is a complex and detailed process that requires special molds and equipment, and the cost of these molds is usually fixed and does not decrease with smaller production volumes.
Mold and sampling costs are significant expenses in custom production, especially for small orders, as the mold cost per unit is much higher. Therefore, the difficulty of amortizing mold costs is a key reason for higher unit prices in small-batch custom orders.
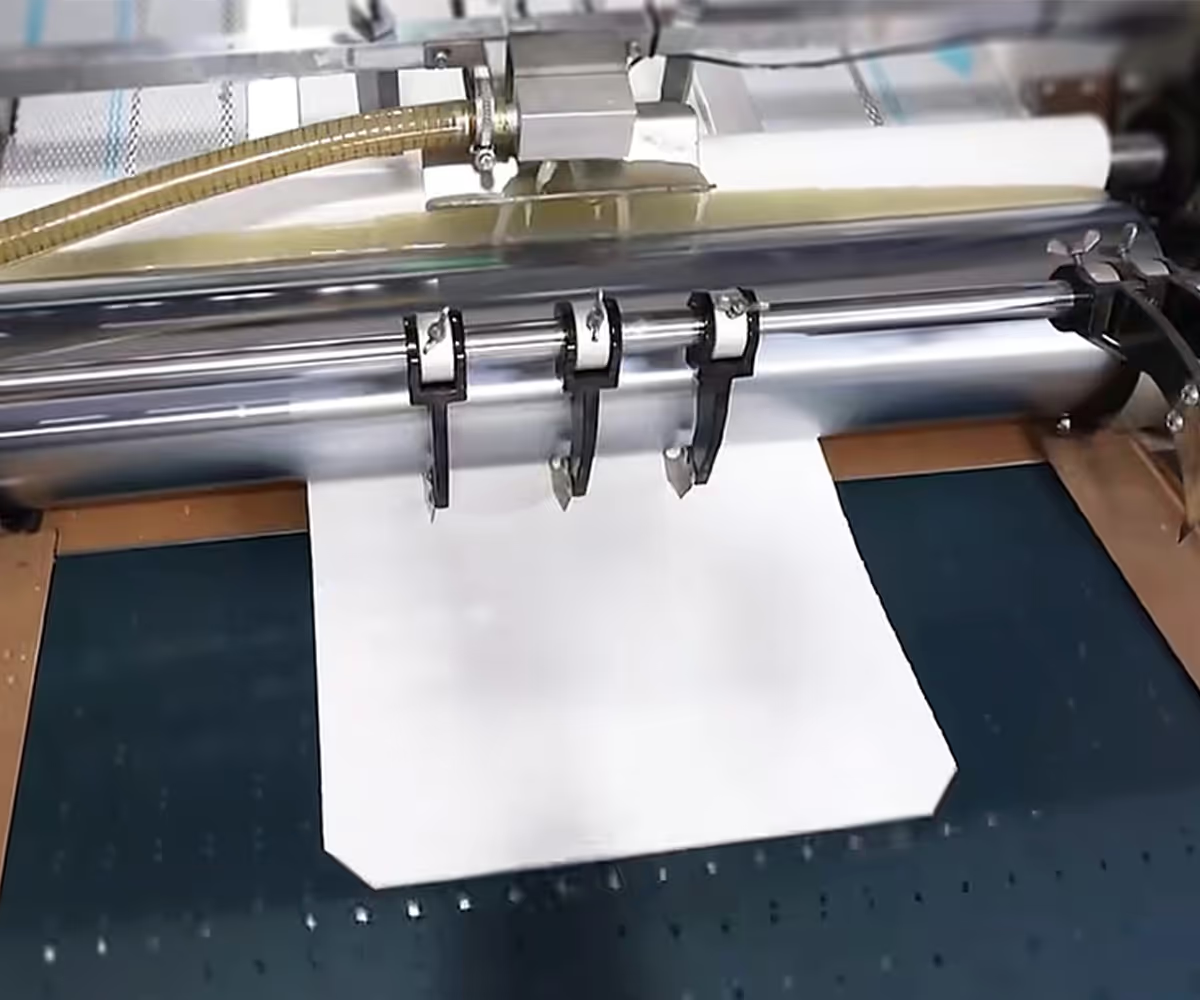
Material Procurement and Inventory: High Cost Pressure for Small Batch Customization
Custom boxes often require more specialized materials, such as specialty paper or unique finishing techniques tailored to the brand's needs. These materials typically need to be specially procured and come at a higher cost than the standard materials used in mass-produced standard boxes, sometimes even involving additional mold costs.
To accommodate smaller custom orders, manufacturers may also face additional inventory pressure. These factors lead to higher unit costs for small-batch custom orders since manufacturers cannot offset costs through bulk material purchases.
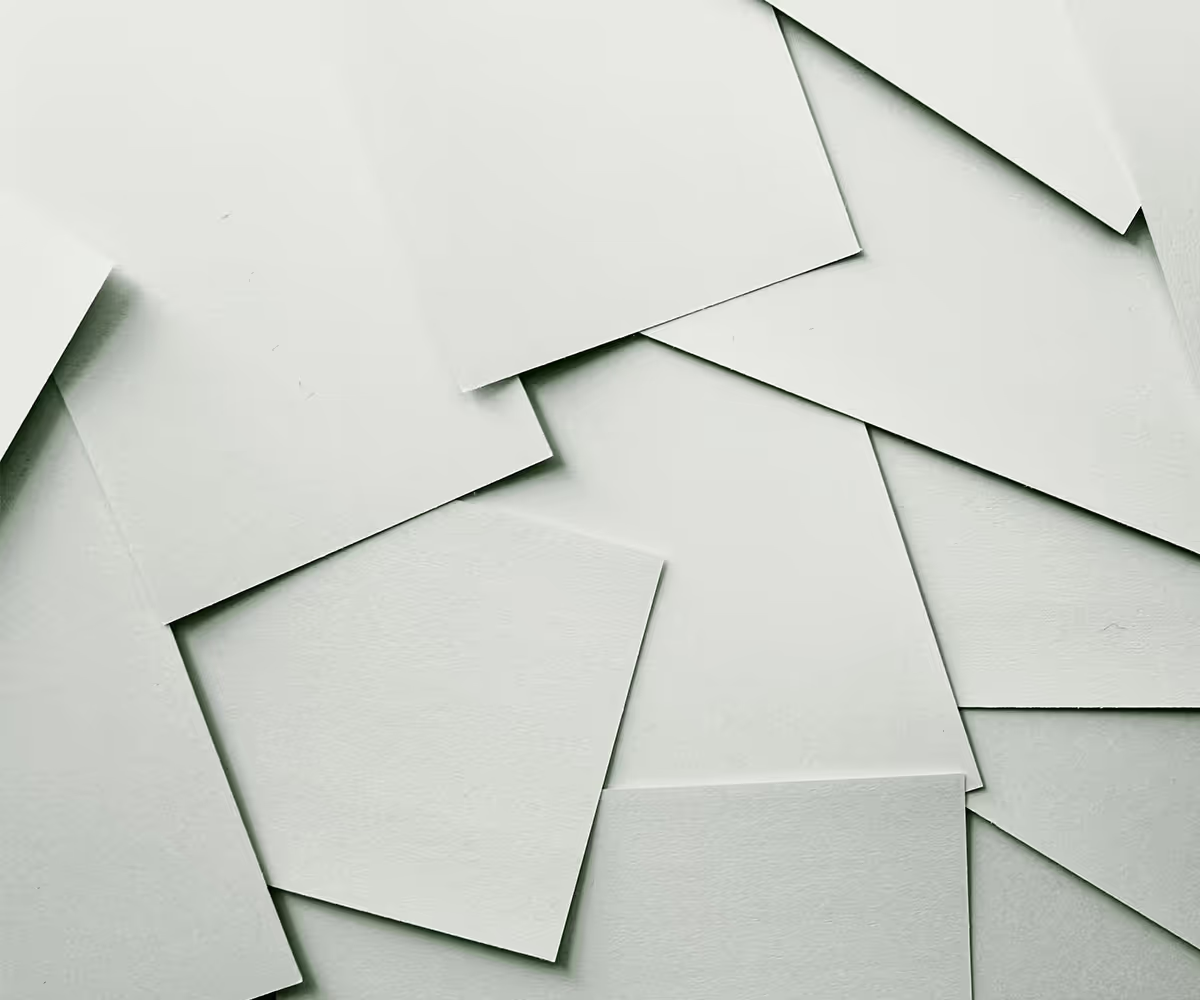
Production Efficiency: Reduced Efficiency in Small Batch Production
In production, standard boxes benefit from high efficiency and economies of scale on the assembly line, where setup and scheduling costs are diluted across a large output. Custom boxes, due to their unique styles and designs, require frequent adjustments to machine settings, resulting in lower production efficiency.
These adjustments increase production time and equipment costs, and for small orders, the downtime, setup, and cleanup time are nearly the same as for larger orders. As a result, the production cost per box increases, leading to a higher unit price.
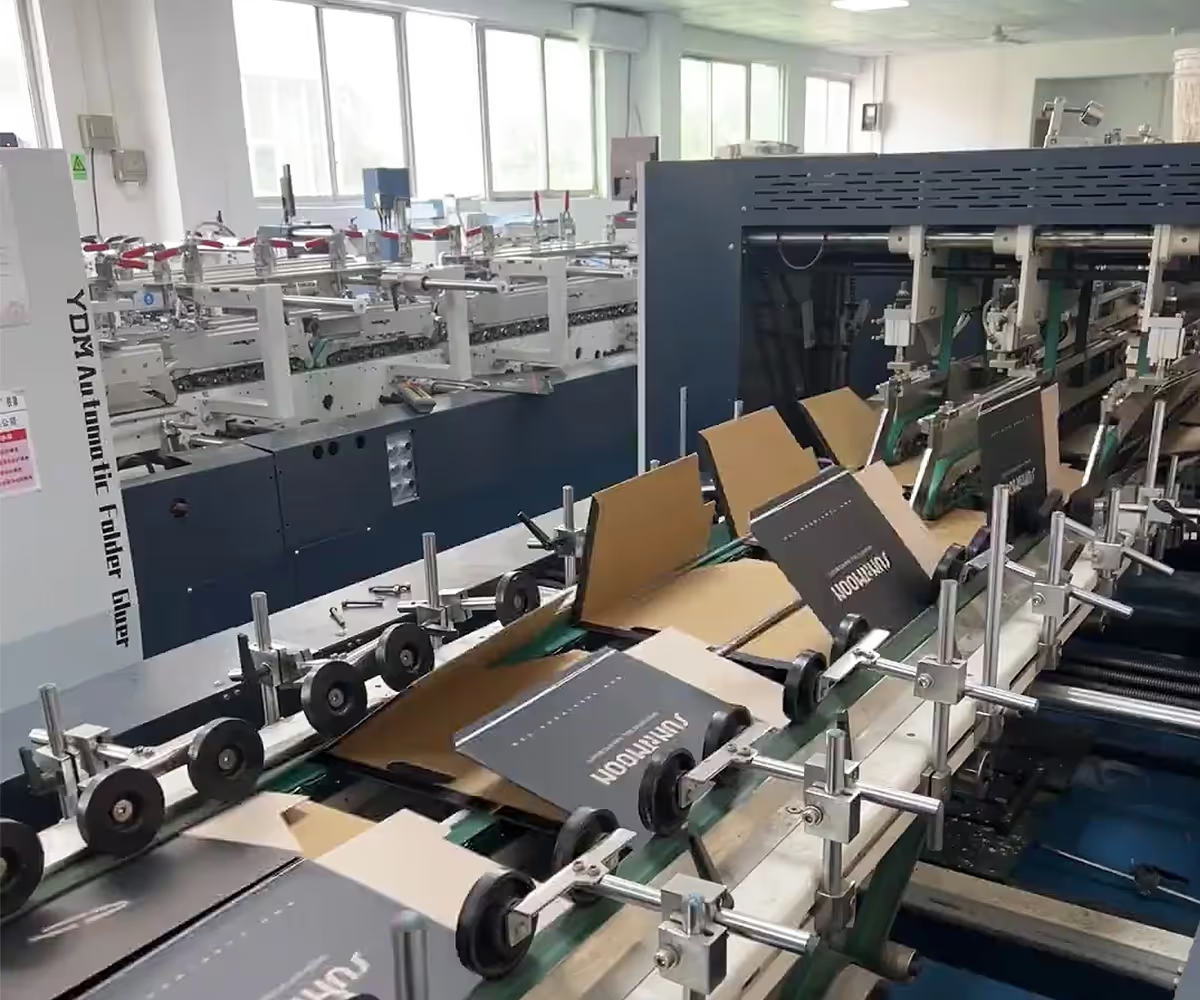
Printing and Finishing: Material Waste in Small Orders
Custom boxes often require special printing techniques, such as hot stamping, embossing, or UV printing, which add extra steps and materials to the production process. Compared to standardized boxes, custom printing can result in more material waste, especially in small-batch production, where setup and waste ratios are higher.
Each batch of custom orders requires individual print setup, and the time and materials spent on these adjustments are particularly significant in small-batch orders. This is another reason for the higher unit price of small-batch custom orders.
Quality Control: Additional Costs from Rigorous Quality Standards
Custom boxes, due to their uniqueness and brand-specificity, usually come with higher quality expectations. Each box must undergo stringent quality checks to ensure the final product is flawless. To meet this standard, manufacturers must invest more time and manpower in quality control.
This rigorous quality control process not only increases production complexity but also raises overall costs. In small-batch orders, these costs are harder to offset through economies of scale, further increasing the unit price.
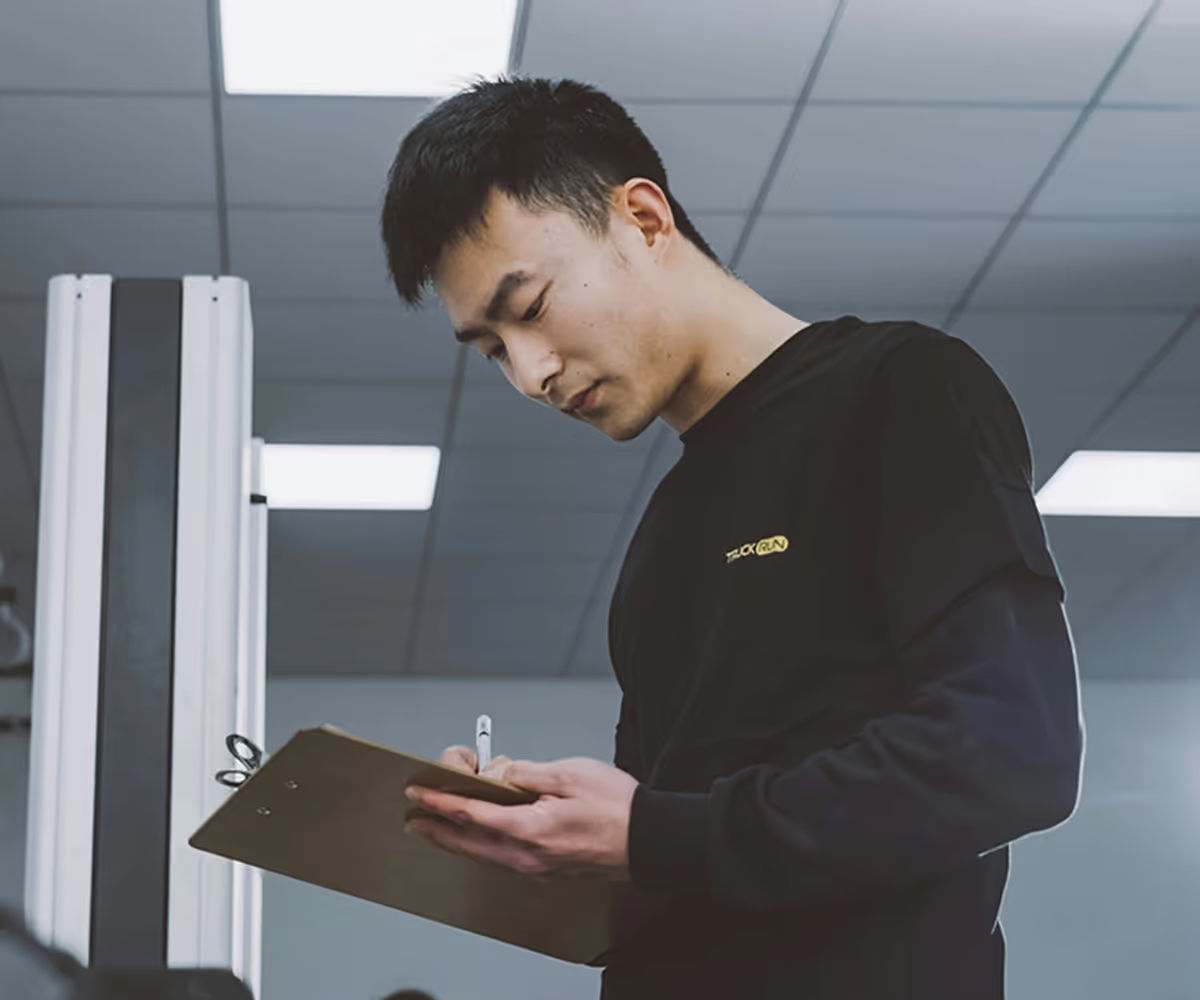
Conclusion
The higher price of custom boxes compared to standard boxes, and the increased unit price with smaller quantities, is due to accumulated costs at various stages. Design, sampling, mold fees, material procurement, production adjustments, printing techniques, and stringent quality control all contribute significantly to the cost of custom boxes. Particularly when clients lack design files, the additional cost of design services further drives up the unit price. Although custom boxes are more expensive, the brand value and market competitiveness they add often far outweigh their cost.
Recommended for you
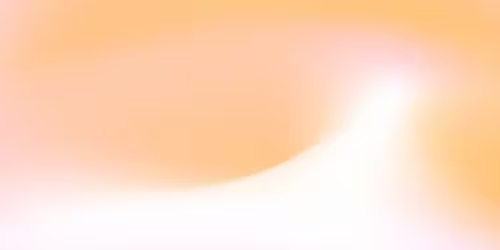