Main Process and Steps of Custom Packaging
Discover the essential steps and processes involved in custom packaging. Learn how to create tailored solutions that meet your unique business needs effectively
Start Customizing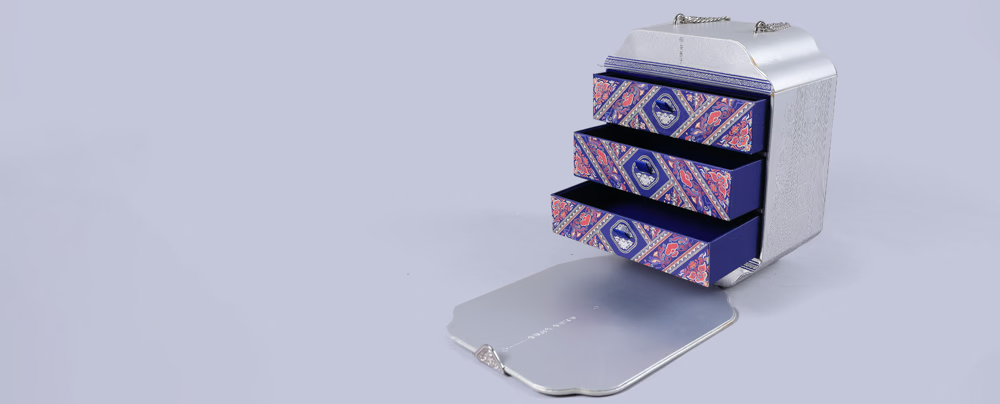
Table of content
In today’s market, custom packaging isn’t just about protecting a product—it’s a key way to show brand value and attract customers. Every custom package is meticulously planned to ensure it’s not only functional but also embodies the unique character of the brand. Below is the complete process from concept to finish custom packaging.
Clarifying Requirements: Understanding Product Attributes and Packaging Needs
The first step in custom packaging is thoroughly understanding the product and brand characteristics. We ask detailed questions about product dimensions, weight, and specific protection needs to ensure the packaging is tailored to the product. Depending on brand positioning, we discuss whether a minimalist style, eco-friendly material, or luxurious look is needed to ensure the packaging visually aligns with the brand’s tone.
In some cases, clients may not provide complete product information, which makes it challenging for designers to determine the dimensions and inner structure. In such situations, we work closely with the client to gather as much information as possible to provide a foundation for structural design and material selection.
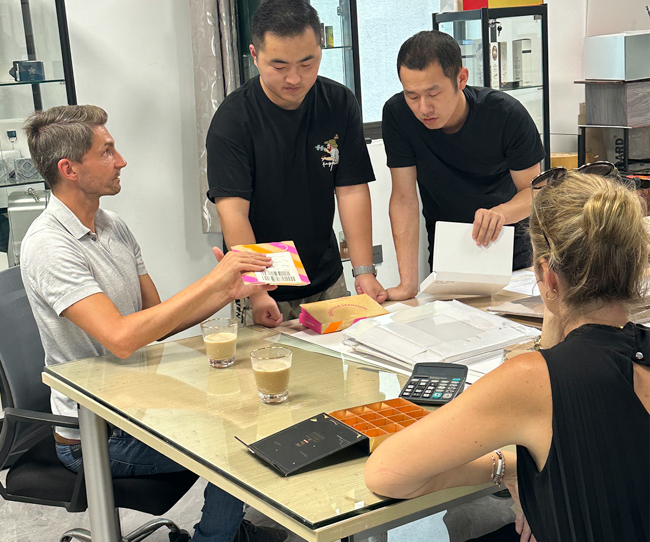
Packaging Product Box Design
From Initial Concept to Detailed Drawings:Design is at the heart of custom packaging as it determines not only the visual appeal but also the user experience. The design process includes several steps:
Structural Design: Our structural designers create packaging that protects the product while offering an unboxing experience. The unboxing process forms the user’s “first impression”, so every layer should lead to an experience of exploration and surprise.
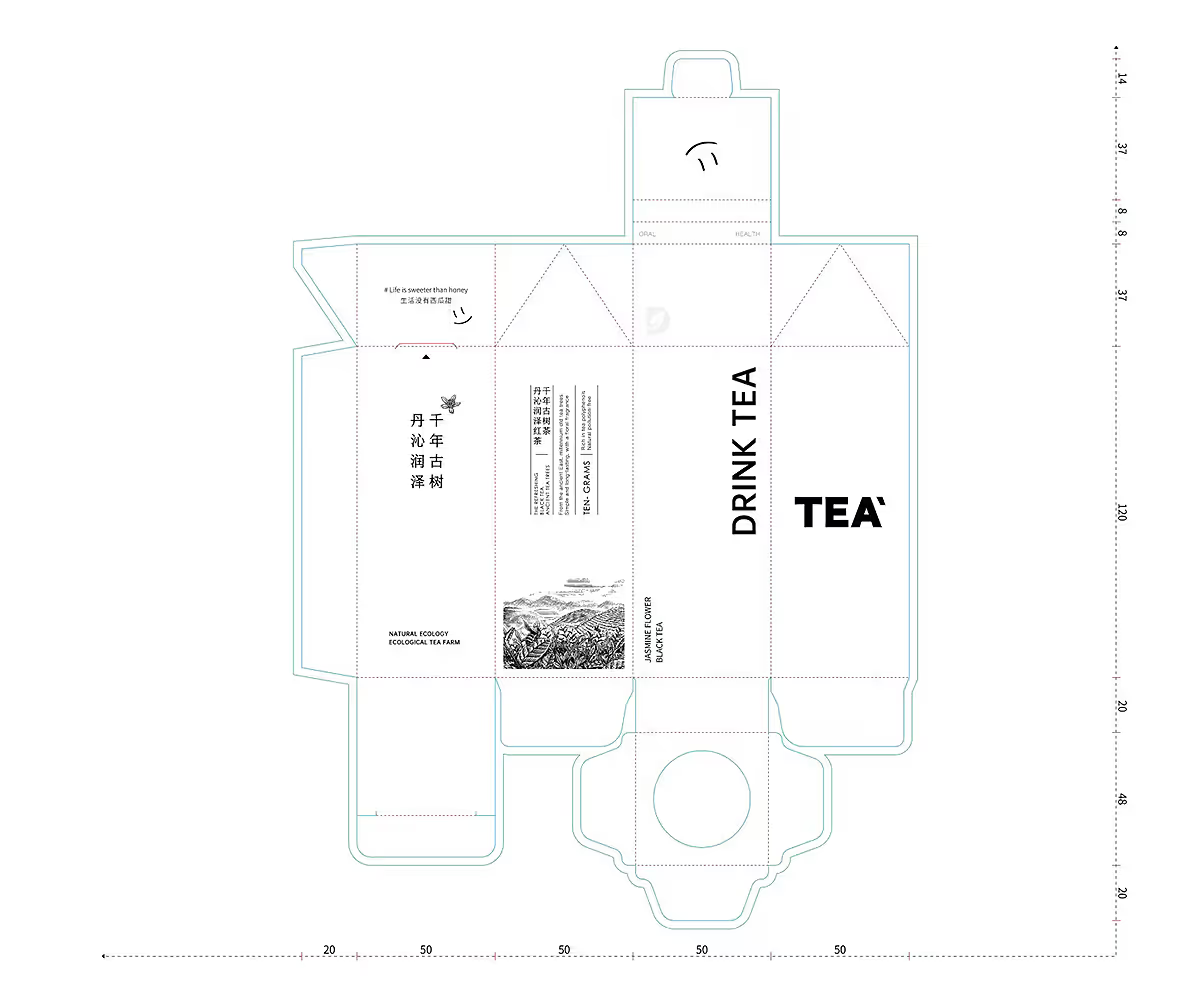
Graphic Design: Once the structural design is finalized, the graphic designer works on the packaging’s visual elements, including brand logos, graphic elements, and text layout, to ensure the packaging is both aesthetically pleasing and reflective of the brand story.
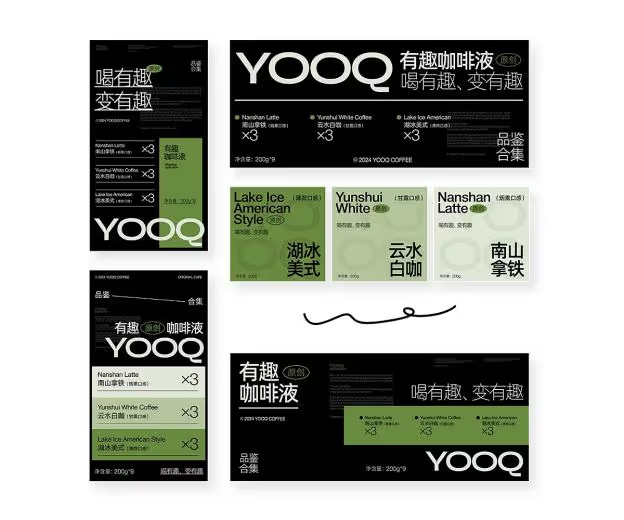
Material and Process Selection: After the graphic design is confirmed, we discuss the materials and processes for the packaging. Packaging is the “outfit” of a product and can be simple or luxurious. The choice of materials and techniques greatly influences the overall effect. For example, by using foil stamping, embossing, or eco-friendly materials, the packaging can better reflect the brand’s values and quality standards.
Material Selection: In-Depth Choice of Materials and Techniques
The choice of material determines the texture, eco-friendliness, and cost of the packaging, while different techniques can add more details. Based on the brand’s style and budget, we recommend various material and technique combinations to achieve the best visual appeal, touch, and sustainability.
Common material options include thick cardboard, corrugated paper, flock lining, etc. Techniques like foil stamping, UV printing, and embossing add dimensionality to the packaging. Different materials and techniques can meet the brand’s diverse design and functionality needs, making the packaging expressive, eco-friendly, and practical.
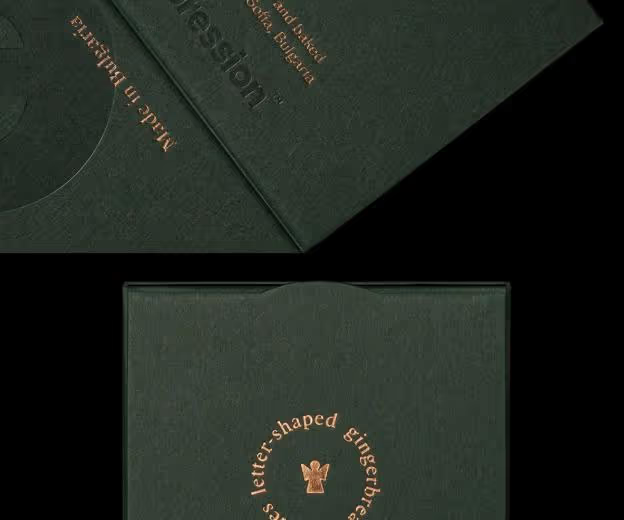
Sampling: Making an Initial Sample
Sampling is a key step in confirming the design effect and structural feasibility. With a sample, the client can see the final product’s actual effect and experience the visual and tactile qualities of the packaging. During this phase, we carefully check the following aspects:
Size and Structure: Ensuring the packaging size fits the product perfectly and the structure is sturdy.
Visual Appeal and Tactile Quality: Testing if the materials and design meet the brand’s requirements and if the texture and colors align with expectations.
Functionality Testing: Verifying the ease of opening and closing, the protection capabilities, and whether it suits transport or display needs.
The sampling phase is crucial to ensure the final packaging aligns with the client’s expectations, so we maintain close communication with the client and make timely adjustments based on feedback.
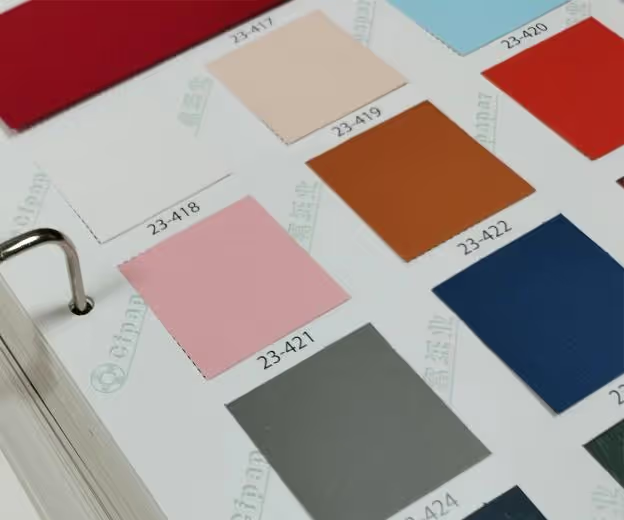
Production: Mass Production and Quality Control
Once the sample is approved, mass production begins. The production phase ensures that the packaging maintains consistency and stability in large-scale production. To achieve a high-quality final product, we take the following steps:
Material Preparation: Ensuring all materials meet standards and are in sufficient supply for a smooth production process.
Mass Processing: Following the design plan confirmed during sampling, we proceed with printing, cutting, and assembling.
Quality Inspection: Conduct strict quality checks during production to ensure every packaging piece is consistent in color, material, and structure, meeting quality standards.
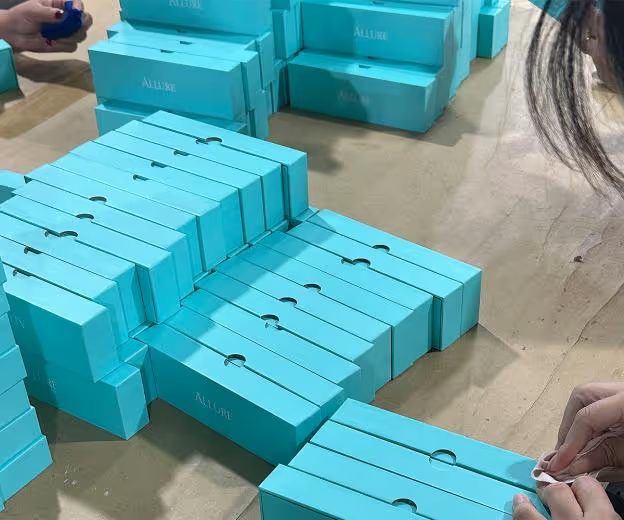
Packaging and Delivery: Final Packaging and Shipping Arrangements
After production, final packaging and delivery is the last step. We carefully package the finished products to ensure they remain intact during transport. Delivery arrangements are made based on the client’s location and schedule to ensure timely delivery.
Final Packaging: Selecting the appropriate packaging method based on product characteristics to ensure they remain undamaged during delivery.
Logistics Arrangements: Choosing reliable logistics providers to ensure safe, timely delivery to the client.
After-Sales Service: We provide necessary after-sales support to ensure client satisfaction and promptly address any feedback or issues.
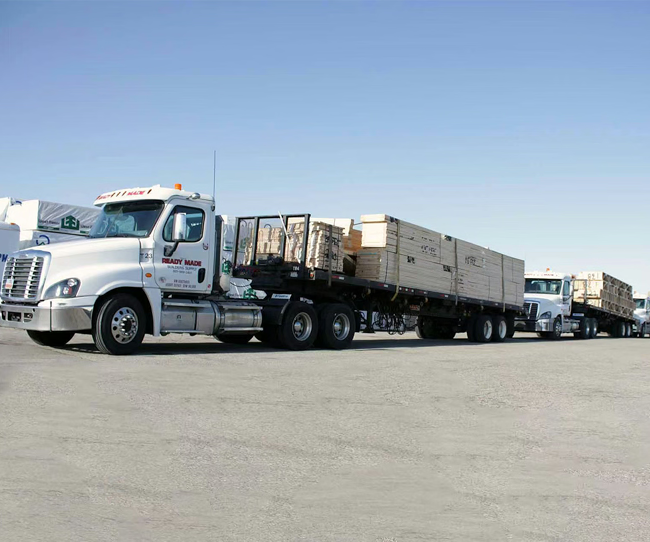
Conclusion
From requirements confirmation, design, material selection, sampling, and production to delivery, each step is indispensable in custom packaging. Details in materials and techniques can create a personalized effect for the brand, making the packaging boxes more appealing. If you want to create a unique packaging solution for your brand, feel free to contact our professional team and give your product exclusive, refined packaging.
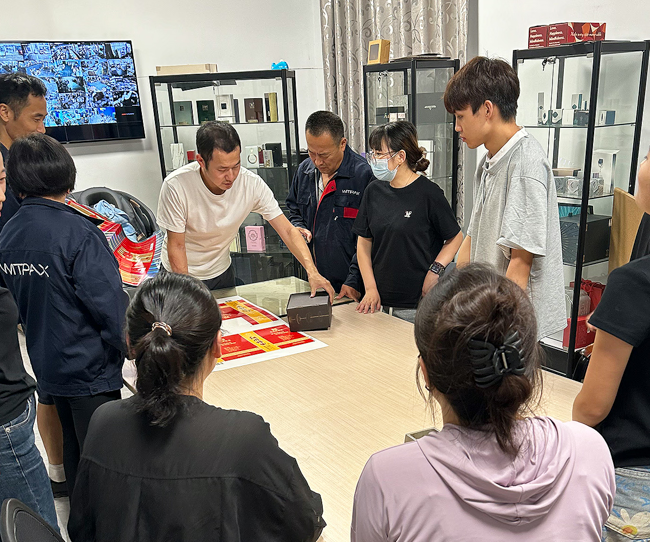
Recommended for you
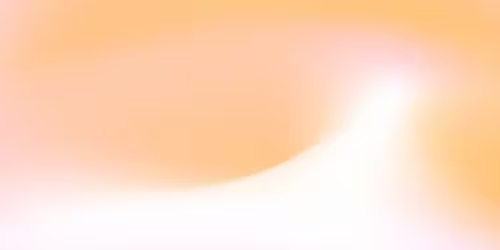